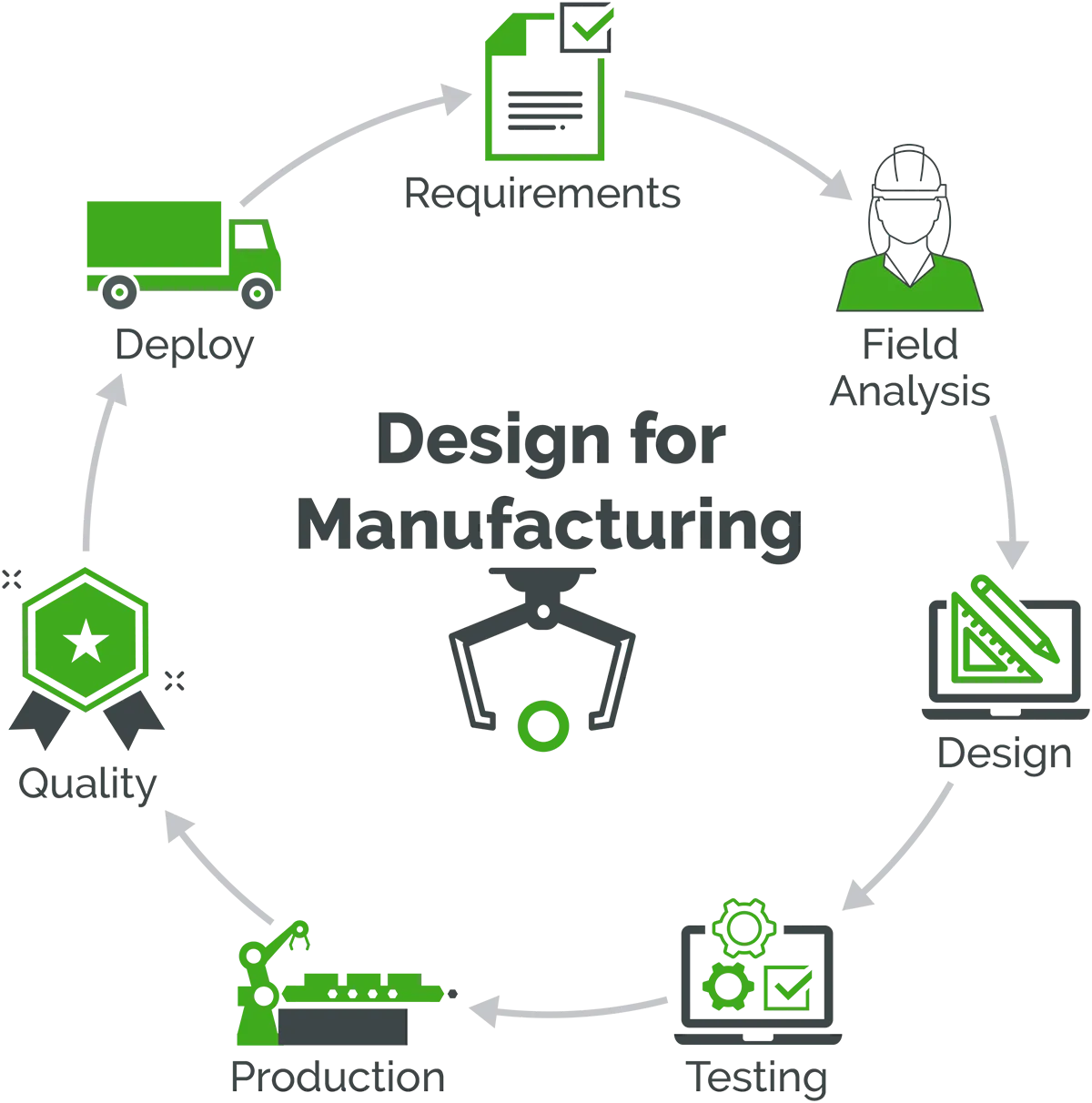
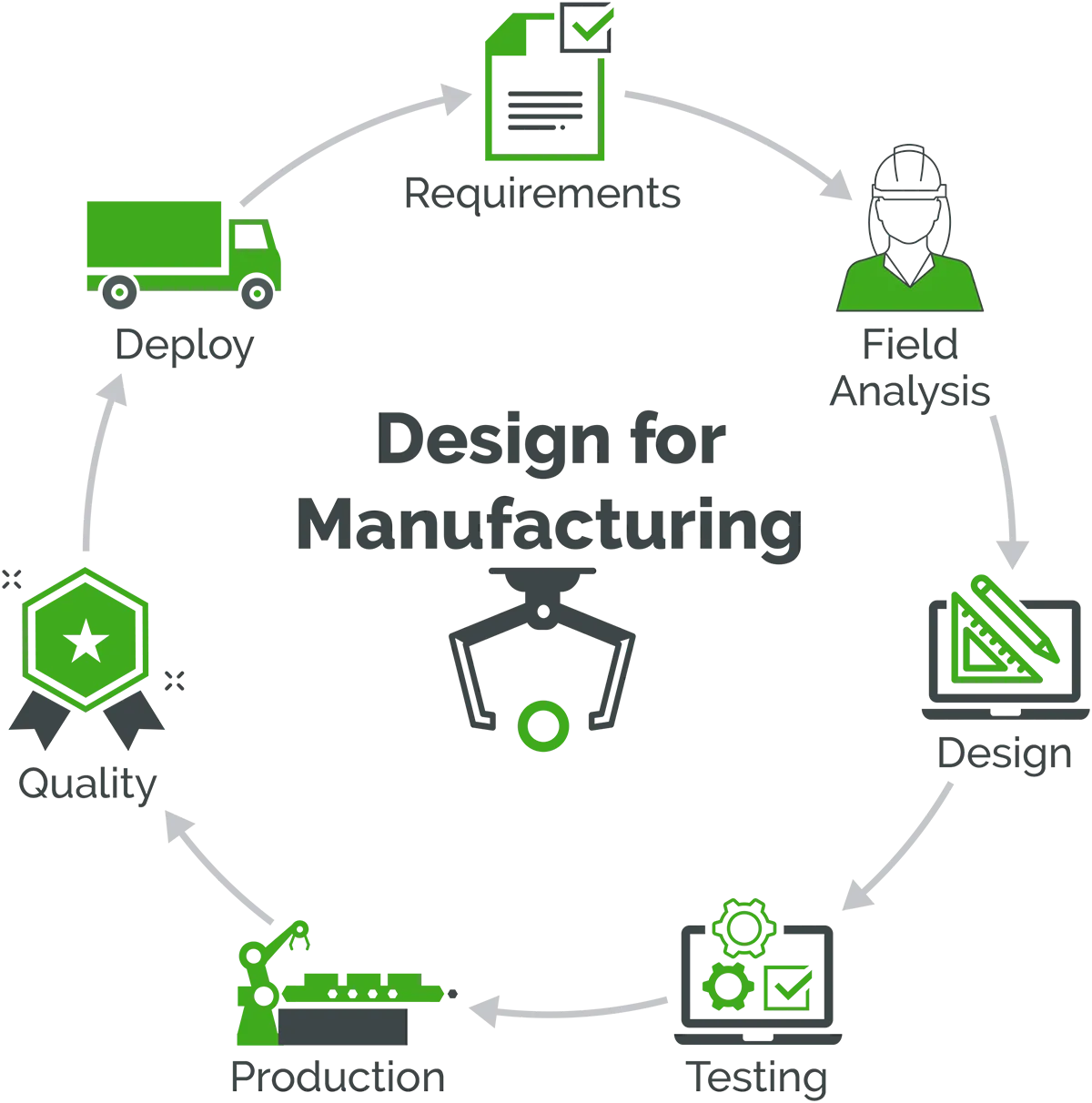
Automated production is transforming medical device manufacturing by improving efficiency, consistency, and scalability while reducing costs and human errors. However, automation only works effectively when products are designed with DfM (Design for Manufacturability) principles in mind. This approach ensures that medical devices are optimized for robotic assembly, automated testing, and mass production from the earliest design stages.
Why DfM Matters for Automated Medical Device Production
Medical devices must comply with strict FDA, ISO 13485, IEC 60601, and MDR regulations, making their manufacturing processes highly complex. Traditional manual assembly increases variability, cost, and risk of defects, while automation ensures repeatability, precision, and cost savings. A well-executed DfM strategy ensures that:
- Devices are designed to be assembled by robots with minimal human intervention.
- Components are selected for automated placement, soldering, and inspection.
- Material choices support automated handling (e.g., pick-and-place, ultrasonic welding).
- Testing and quality control can be seamlessly integrated into the automated workflow.
Key DfM Considerations for Automated Medical Device Production
1. PCB Design for Automated Assembly (SMT & Pick-and-Place)
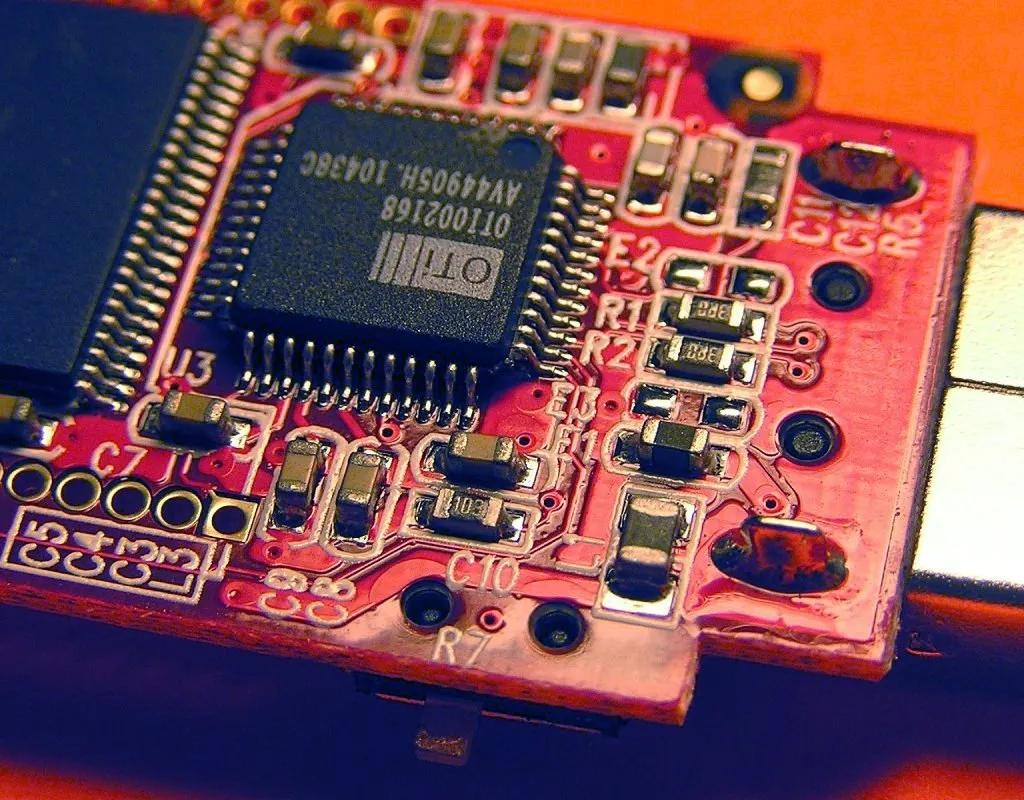
Printed Circuit Board (PCB) design is a major cost driver in wearables, implants, and handheld medical devices. Optimizing PCBs for Surface Mount Technology (SMT) and automated placement improves efficiency.
- Use standardized component sizes (0402, 0603) to ensure compatibility with pick-and-place machines.
- Minimize the number of PCB layers to reduce fabrication costs while maintaining signal integrity.
- Ensure proper spacing and orientation of components to prevent errors in automated soldering.
- Use fiducial markers for accurate robotic alignment.
Example: A wireless biosensor startup reduced PCB assembly time by 30% by aligning all passive components in a single direction, improving automated soldering efficiency.
2. Mechanical Design for Robotic Assembly
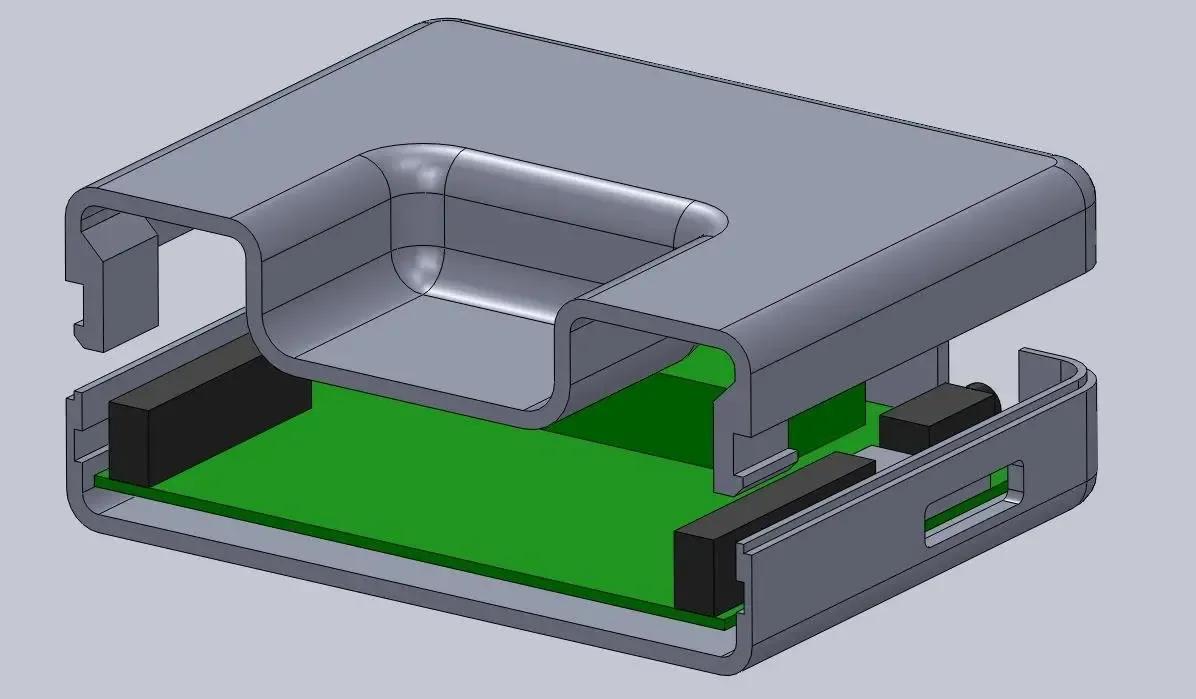
Medical devices with complex enclosures, connectors, or moving parts must be designed for robotic assembly:
- Avoid intricate screw assemblies—use snap-fits or ultrasonic welding instead.
- Use self-aligning parts to prevent errors in automated assembly.
- Minimize small or delicate components that require manual handling.
- Select materials that support robotic gripping and automation (e.g., molded plastics instead of hand-machined metal parts).
Example: A disposable drug delivery system switched from manual screw fastening to ultrasonic welding, reducing assembly cost per unit by 40% while improving sterility.
3. Connector and Cable Management for Automation
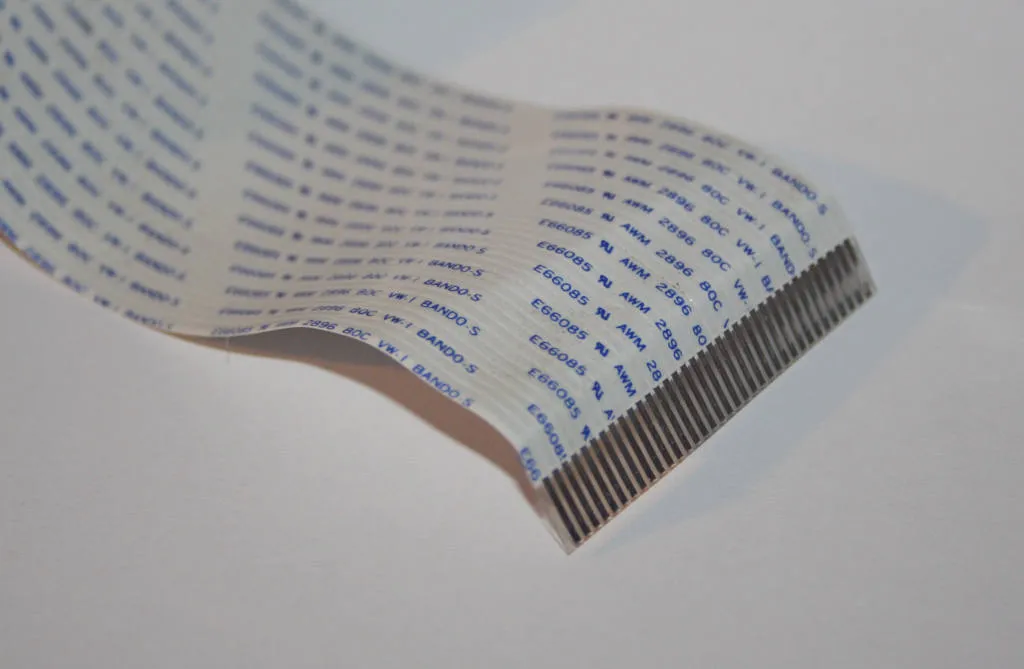
Cables, connectors, and wiring are common bottlenecks in automation. Simplifying these elements improves efficiency.
- Eliminate unnecessary connectors and use PCB-to-PCB edge connections where possible.
- Use flat flexible cables (FFCs) or board-to-board connectors instead of hand-soldered wires.
- Design connectors with self-aligning features to ensure robotic insertion.
Example: A patient monitoring device eliminated internal wiring by integrating rigid-flex PCBs, improving reliability and automation compatibility while reducing assembly time by 50%.
4. Material Selection for Automated Manufacturing
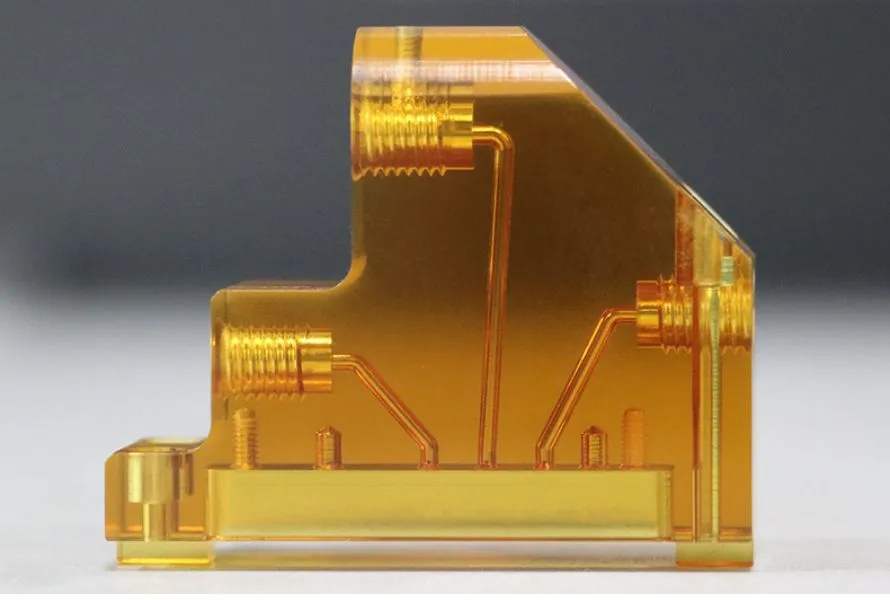
Material choice affects both manufacturability and compliance with ISO 10993 biocompatibility and sterilization standards.
- Opt for injection-molded medical-grade plastics instead of machined parts for higher scalability.
- Use heat-resistant polymers (e.g., PEEK, Ultem) to withstand automated soldering and sterilization processes.
- Select materials that are compatible with high-speed robotic assembly (e.g., non-static, non-sticky surfaces).
Example: A wearable insulin pump replaced hand-assembled metal casings with injection-molded PEEK, reducing cost by 35% while ensuring compatibility with robotic assembly lines.
5. Automated Testing and Quality Control Integration
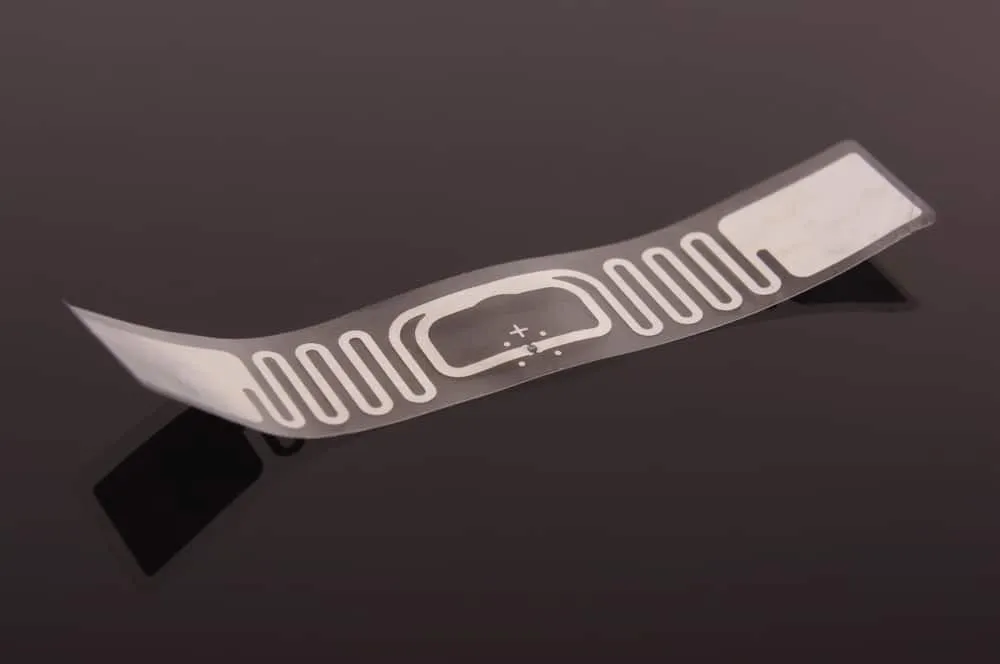
Regulatory compliance requires 100% inspection and traceability in medical device production. Designing for automated testing reduces human error and cost.
- Incorporate test points and self-diagnostics in PCB design for automated electrical testing.
- Use machine-readable barcodes or RFID tags for tracking and quality control.
- Design products for non-contact optical or ultrasonic inspection instead of manual measurement.
Example: A digital stethoscope manufacturer integrated built-in self-test circuits into their design, enabling automated testing that cut QA costs by 25%.
Benefits of DfM for Automated Medical Device Production
- Lower Manufacturing Costs – Automation minimizes labor costs and increases yield.
- Higher Production Scalability – Robots work at consistent speeds without fatigue, enabling higher throughput.
- Improved Product Consistency – Automated assembly eliminates human error, ensuring better quality.
- Faster Time to Market – Efficient design reduces rework and accelerates regulatory approval.
- Enhanced Regulatory Compliance – Automated testing and traceability simplify audits and FDA submissions.
How ITR VN Helps Medical Device Companies with DfM for Automation
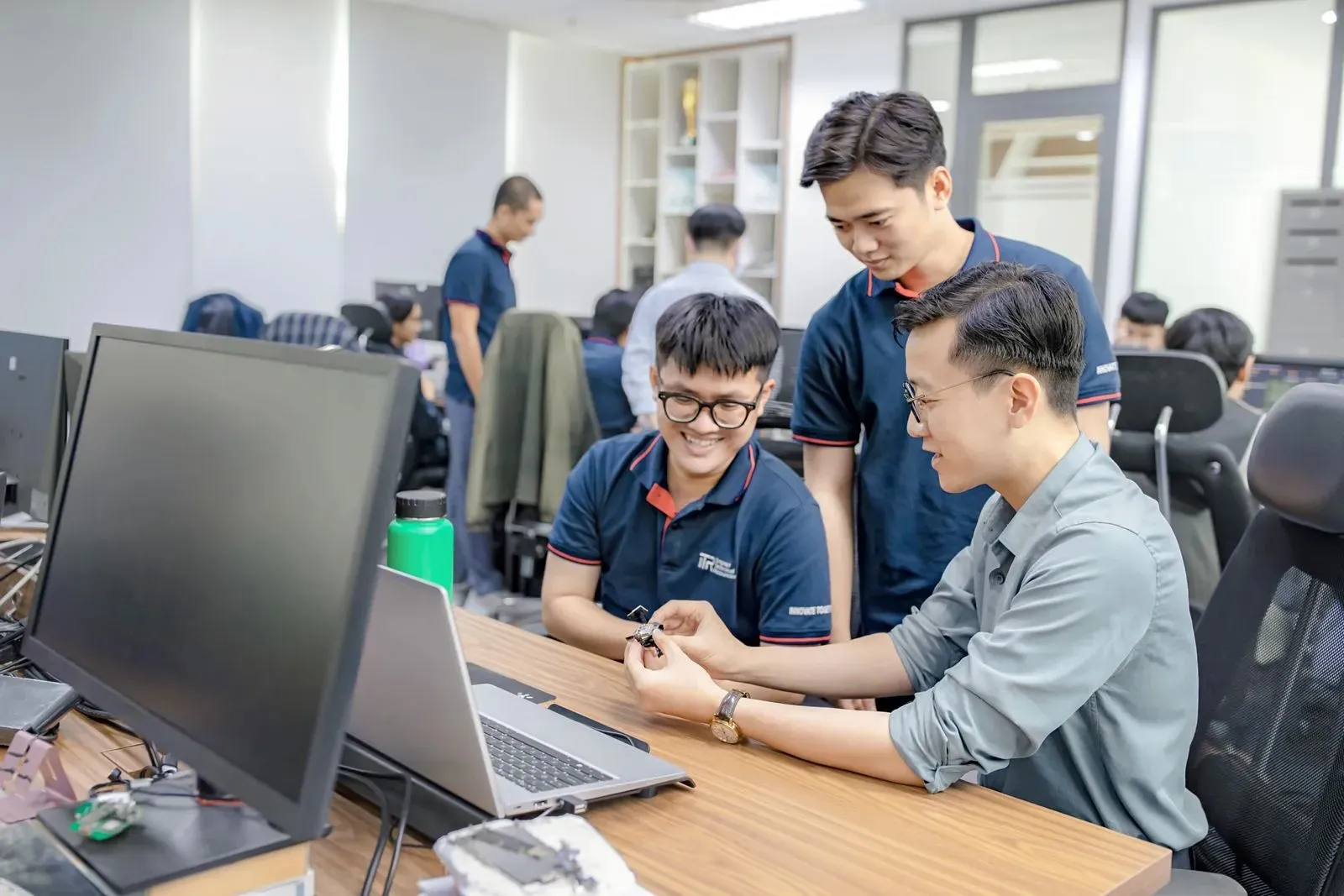
At ITR VN, we specialize in designing medical devices optimized for automated production, ensuring:
Early DfM reviews help prevent costly rework by optimizing PCBs, enclosures, and connectors for robotic assembly, selecting materials that are both automation-friendly and biocompatible, and ensuring seamless integration with Contract Manufacturers (CMs) for cost-effective mass production.By partnering with ITR VN, MedTech companies can design smarter, scale faster, and maintain the highest regulatory and quality standards while keeping costs under control.
Ready to optimize your medical device for automated production? Contact ITR VN today to discuss how our DfM expertise can help bring your next-gen medical device to market faster and more efficiently.